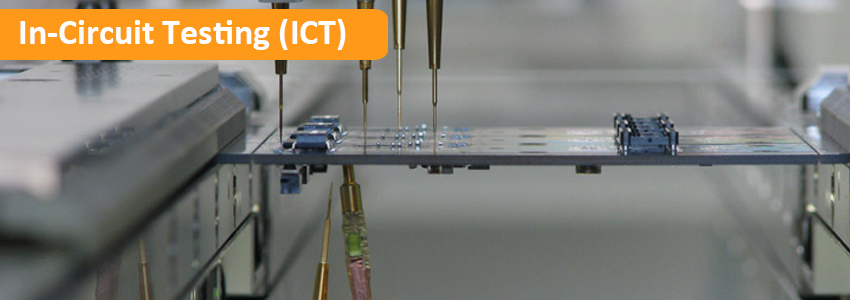
As a Turnkey PCB Assembly Manufacturer and Supplier, Fuchuangke Technology wants all of our customers to be fully confident that their PCB assemblies manufactured by us are working order before they are shipped out from our SMT assembly production facility. We conduct a variety of strict quality control procedures at every stage of the printed circuit board (PCB) assembly process in order to provide our customers this confidence. From standard services such as Visual Inspection and AOI (Automated Optical Inspection), to advanced measures such as X-ray Inspection, and FCT (Functional Testing), each method comes with its own advantages. When customers require a complete and meticulous confirmation of their assembled PCBs, they turn to our most meticulous testing method ICT (In-Circuit Testing).
In-Circuit Testing (ICT) service is often confused with FCT, and indeed the two have some notable similarities: both are performed after AOI and visual inspections, and both involve a quality assurance technician personally inspecting the PCB assembly boards through the use of test instruments and/or software. The main difference between the two testing methods is that FCT is a so-called “black box” testing method, while ICT is a “white box” method. Simply put, FCT looks for overall functionality of a product without regard to the specifics of its inner workings, while ICT pays attention to individual voltage and current levels throughout the PCBA, and might include step-by-step program execution.
Since ICT works on the component level, it can help to localize and issues that may be present on the board, and narrow down the cause to a particular device. This can be extremely valuable in troubleshooting complex Prototype PCB Assembly projects where the design is not yet 100% verified. If any of the PCBs do not pass testing, we can often provide targeted board-level rework to potentially save the batch. Our test engineers will issue a DFA (Design for Assembly) recommendation form to the customer after the ICT process, and our quality assurance engineering team will create an 8D Quality Assurance Report for internal process improvement.
We take pride in working closely with our customers to provide flexible services that can be tailored to their individual needs. Our engineering teams will review your specific test requirements for the project in question, set up all of the needed equipment, develop a testing workflow, and design a test jig if necessary. We are equipped with adjustable DC bench power supplies, 200 MHz digital oscilloscopes, arbitrary signal generators, LRC multimeters, and universal IC programmers to handle any type of project.
Our ICT Specifications
TR5001E Tester Specifications | |
Analog/hybrid test points | 3200 analog or maximum digital test points: 1600 |
Operating System | Microsoft® Windows compatible PC, Windows 7-10 |
Fixture Type | Offline press type fixture |
Standard Testing Components | |
Analog Test Hardware | 6-wire measurement switching matrix |
Programmable AC/DC/DC High voltage and current sources | |
AC/DC voltage, DC current measurement, frequency | |
Component R/L/C measurement | |
Optional Components | |
Analog Hardware | TestJet vectorless open circuit detection |
Arbitrary Waveform Generator | |
Digital Testing | Non-multiplexing 1:1 per pin architecture with independent per-pin level setting |
DUT power supplies: 5 V@3 A, 3.3 V@3 A, 12 V@3A, -12 V@1 A and 24 V@3 A | |
Programmable DUT power supplies: 75 V / 8 A max, 200W maximum output power | |
Includes BScan Chain Test, BScan Cluster Test, BScan Virtual Nails Test, BScan Virtual Chain Test and IEEE1149.6 Test |
|
On-board Flash, EEPROM, MAC programming | |
Yield Management System | YMS 4.0 |
Board Handling | |
Max PCB Size | Standard: 420 x 300 mm |
Option: 500 x 350 mm or larger |
If you are in need of a tailored ICT solution for your next PCB Assembly project, please feel free Contact Us with your requirements or with any questions you might still have about our ICT process.
PCB Assembly Quick Quote
FR-4 PCB Quote Flexible PCB Quote Rigid-Flex PCB Quote IMS PCB Quote