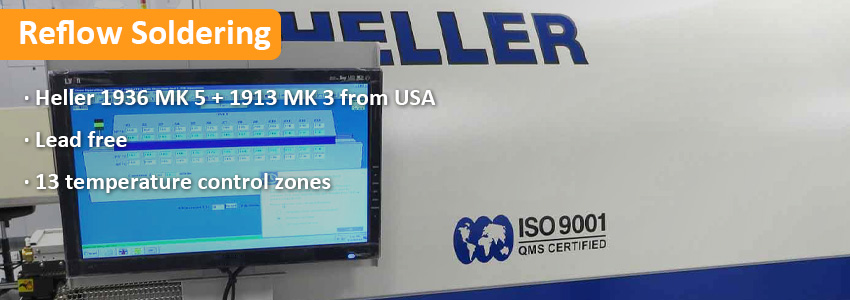
Surface mount devices (SMDs) are rapidly replacing thru-hole components in commercial electronic manufacturing. As a result, more and more components are available only in surface mount packages. The SMDs are soldered onto the bare PCBs with Infra-red reflow soldering, which becomes the most widely used and very effective technology of attaching SMD components to bare PCB boards.
The purpose of reflow soldering is to create acceptable solder joints, which provide a strong and reliable means of connecting components electronically and mechanically within the PCB circuitries, by first pre-heating the components, bare PCB and solder (Tin) at the same time, and then melting the Tin without causing any damage by the overheating in the reflow soldering period.
Features of Heller Reflow Oven 1913 Mark III:
- 13 Temperature Control Zones
- Maximum Board Size: 508mm x 610mm (20’’x24’’)
- Minimum/Maximum Board Width: 50mm (2’’) / 457mm (18’’)
- Heated Tunnel Length: 3556mm (140’’)’’
- Accuracy of Temperature Control: +/-0.1°C
- Cross-Belt Temperature Tolerance: +/-3.0°C
- Temperature Range Standard: 25-350°C
- Numbers of Cooling Zones Standard: 3
For PCB assembly, reflow soldering technology has been used for many years, and reflow soldering is now able to provide unparalleled and high-quality soldering that can meet the requirements to nowadays mass production of electronic hardware. Using reflow soldering technology for PCB Assembly, it is possible to reliably solder SMDs, particularly those with very fine pitch leads.
The bare PCBs through solder paste printing and SMD components placing on the solder paste, then become “components glued PCBs”, which will then move to the reflow soldering Oven. Before moving to the oven, we need to setup the correct reflow oven temperature profile upon analysis of the temperature of the reflow tunnel or chamber, the temperature under the pads of the main components and tunnel speed.
Reflow consists of a few individual processes, which are required to ensure that the PCB boards are brought up to the correct temperature for reflow soldering without applying any unacceptable levels of thermal shock. Only with correct profiling the temperature of the reflow tunnel or chamber, we then move the PCBs to the oven to ensure that the resulting solder paste are of the highest quality. The 4 stages normally used are as following:
- Preheat: The PCB boards need to be brought steadily up to the required temperature. If the rate is too high, then the PCB boards or the components may be damaged by the thermal stress. Additionally, if the printed circuit board is brought to temperature too slowly then the PCB boards may not reach the required temperature, which will result that some components will be cool soldering. The temperature rise rate that is often used for infra-red reflow soldering is between 2 and 3°C per second, although rise down to 1°C per second may be used on some PCB assembly projects.
- Thermal Soak: Having brought the PCB boards up to temperature it next enters what is often termed a thermal soak area. Here the card is maintained at temperature for 2 reasons. One is to ensure that any areas that are not adequately heated because of shadowing effects come up to the required temperature. The other is to remove the solder paste solvents or volatiles and to activate the flux.
- Reflow: The reflow area is the area of the soldering process where the highest temperature is reached. It is here that the solder is caused to melt and create the required solder joints. The actual reflow process involves the flux reducing the surface tension at the junction of the metals to accomplish metallurgical bonding, allowing the individual solder paste spheres to combine and melt.
- Cooling: The cooling for the PCB boards after reflow must be accomplished in a way that does not cause stress to the components. Proper cooling inhibits excess intermetallic formation or thermal shock to the components. Typical temperatures in the cooling zone range from 30-100°C. The temperature in this zone creates a relatively fast cooling rate and this is chosen to create a find grain structure in the solder to provide the most mechanically sound joint.
Click the Quick Quote buttons below, you can turn to the different PCB quote pages. Just fill in the PCB specifications, upload Gerber files, BOM, Assembly Drawing and Pick-and-Place file, you will get quick quote of PCB board and PCB Assembly.
FR-4 PCB Quote Flexible PCB Quote Rigid-Flex PCB Quote IMS PCB Quote